Follow-up Scoop!” Shocking Video of “Big Motor,” the Leading Used Car Dealer, Punching Holes in Customers’ Tires
Former mechanic angrily accuses the giant company, which boasts annual sales of 700 billion yen, of gross negligence.
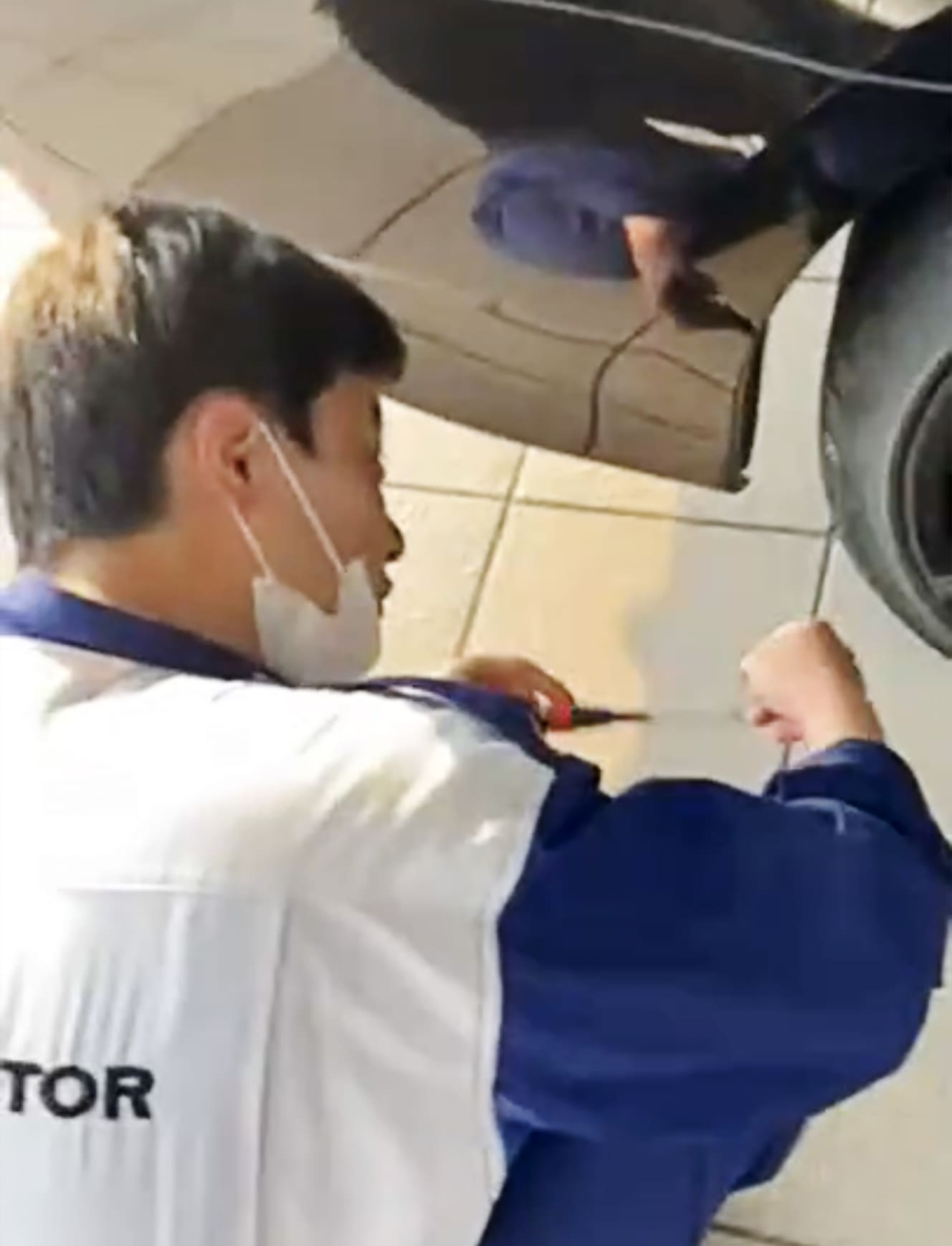
You have to think about how you want your picture to look.
After carefully explaining how to take pictures to be submitted for the insurance company’s review, the man stared at the side of the tire, looked for a point, and stuck a screw into the tire with a gulp. He then used a screwdriver to grind and tighten that screw with great force. Just 10 seconds later, the tire went flat with ease.
Big Motor, a used car sales company with approximately 260 stores nationwide, 6,000 employees, and annual sales of over 700 billion yen, has been exposed to a string of fraudulent activities. Last February, the company’s Biwako Moriyama store in Shiga Prefecture was ordered by the Kinki District Transport Bureau to suspend business operations due to unauthorized modifications. In February of this year, the Karatsu branch in Saga Prefecture, and in March, the Kumamoto Hamasen branch in Kumamoto Prefecture, were suspended from receiving safety standard compliance certificates and their designation as private vehicle inspection stations by the Kyushu District Transport Bureau for fraudulent vehicle inspections.
Amidst this situation, this magazine obtained even more shocking evidence of fraud. This is the “hole-punching video” described at the beginning of this article. Mr. A, who provided the video, had worked at the Kumamoto Hamasen branch, which was in the middle of the controversy, for about two years since 2007, and was in charge of the maintenance department and held other important positions.
The video was shot by Mr. A in June 2009 under the false pretense of “learning the job” in order to preserve evidence of wrongdoing. The man shown in the video was the plant manager at the time, and in the 40-second video, he gives detailed instructions to the insurance company to make the tire puncture look natural. In the video, the plant manager screws on the tire while,
‘If you film it from here, it will look like it has grooves (so that even a worn tire is not worn down within the insurance coverage).’
Then you can shoot the brand name.”
He continues to work flatly while giving instructions to the customer. After less than 10 seconds, the tire went flat.
The video is a lecture on how to intentionally puncture a tire. It was a customer’s car that had a hole in it. This car was chosen as the target for puncturing because the tire was so worn down that the grooves were gone and it could have been punctured at any time. The purpose of the puncture is to charge a labor fee. The tires themselves are not at the expense of the customer because in many cases they are covered by insurance, but we do charge a labor fee for the replacement; it is about 3,000 yen per tire, but when we replace them, we usually replace four tires at once, so we make a sale of more than 10,000 yen. Not everything was done this way, but the labor charge alone generated 200,000 to 300,000 yen per month.
It is said that even more malicious fraud was taking place at other stores. According to what I have heard directly from fellow mechanics, they are cutting out insurance money. They would replace the tires with cheaper ones after getting a flat tire, while claiming to the insurance company that they had switched to the latest high-end model. The difference is their entire profit.
The insurance company’s inspection is basically a photo check, so it is not difficult to disguise a flat tire as a spontaneous one.
I protested to the plant manager, but he would not listen to me. I never did the ‘puncturing’ myself, but I was aware of the crime but could not stop it. I always felt guilty.”
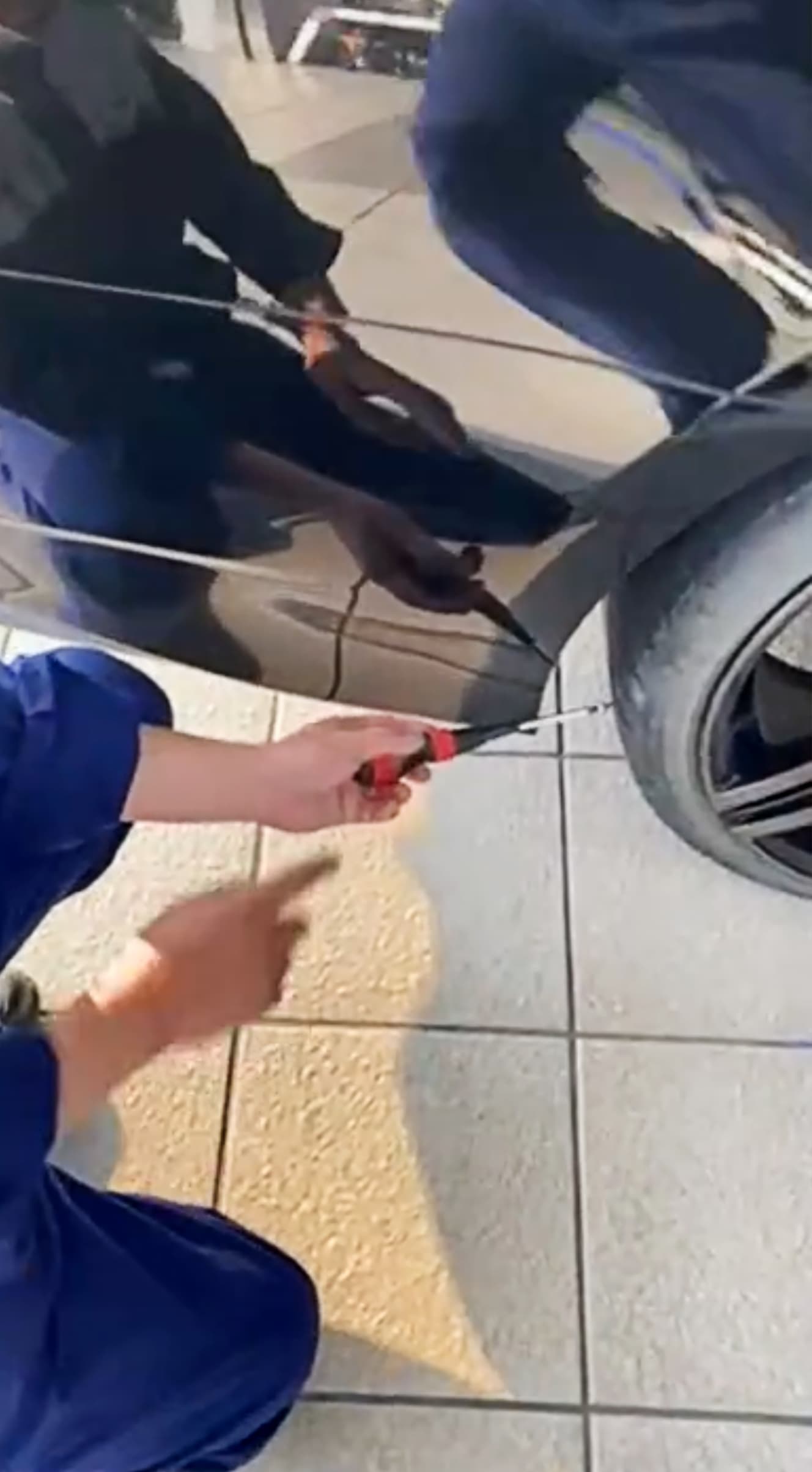
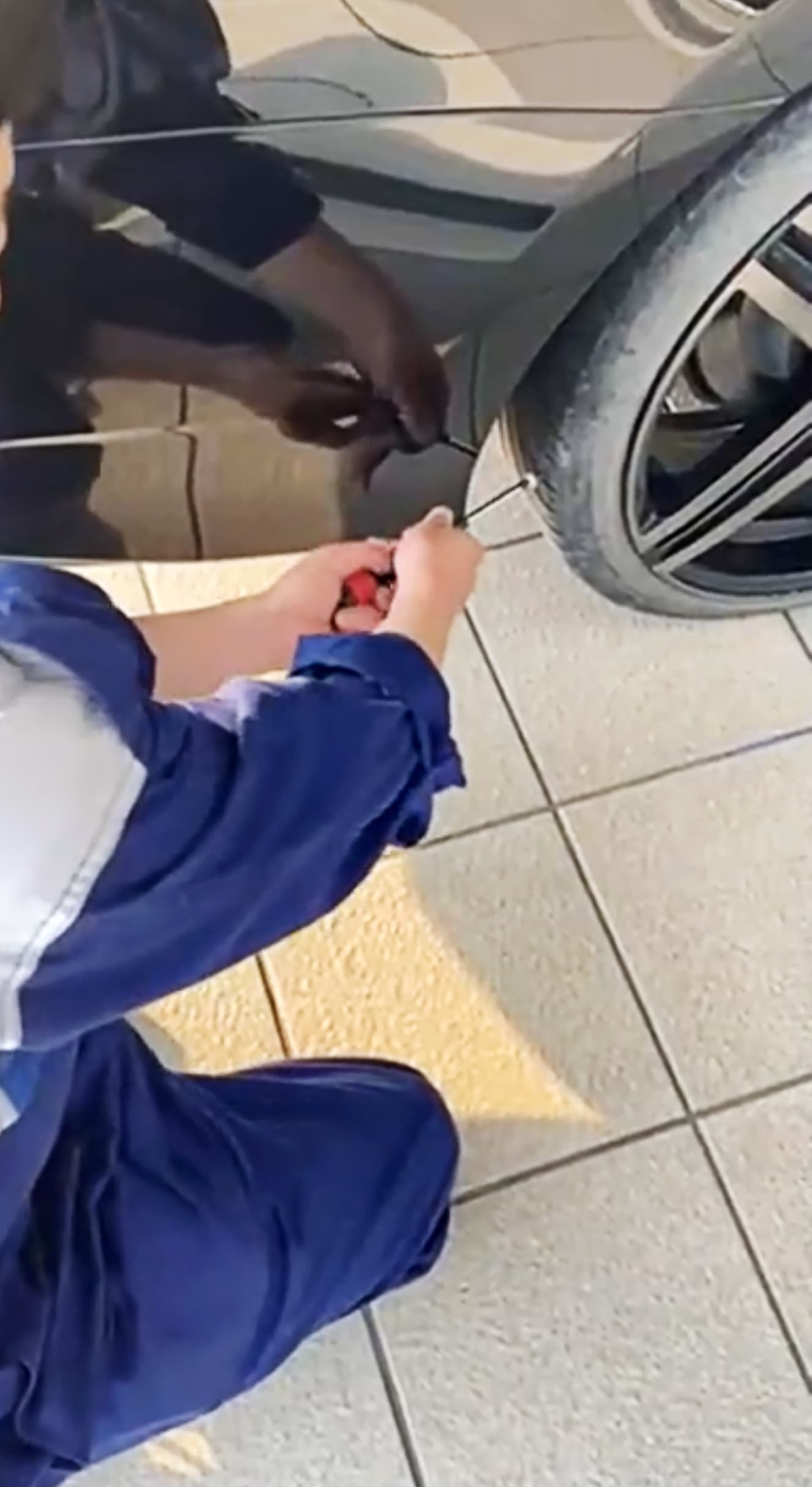
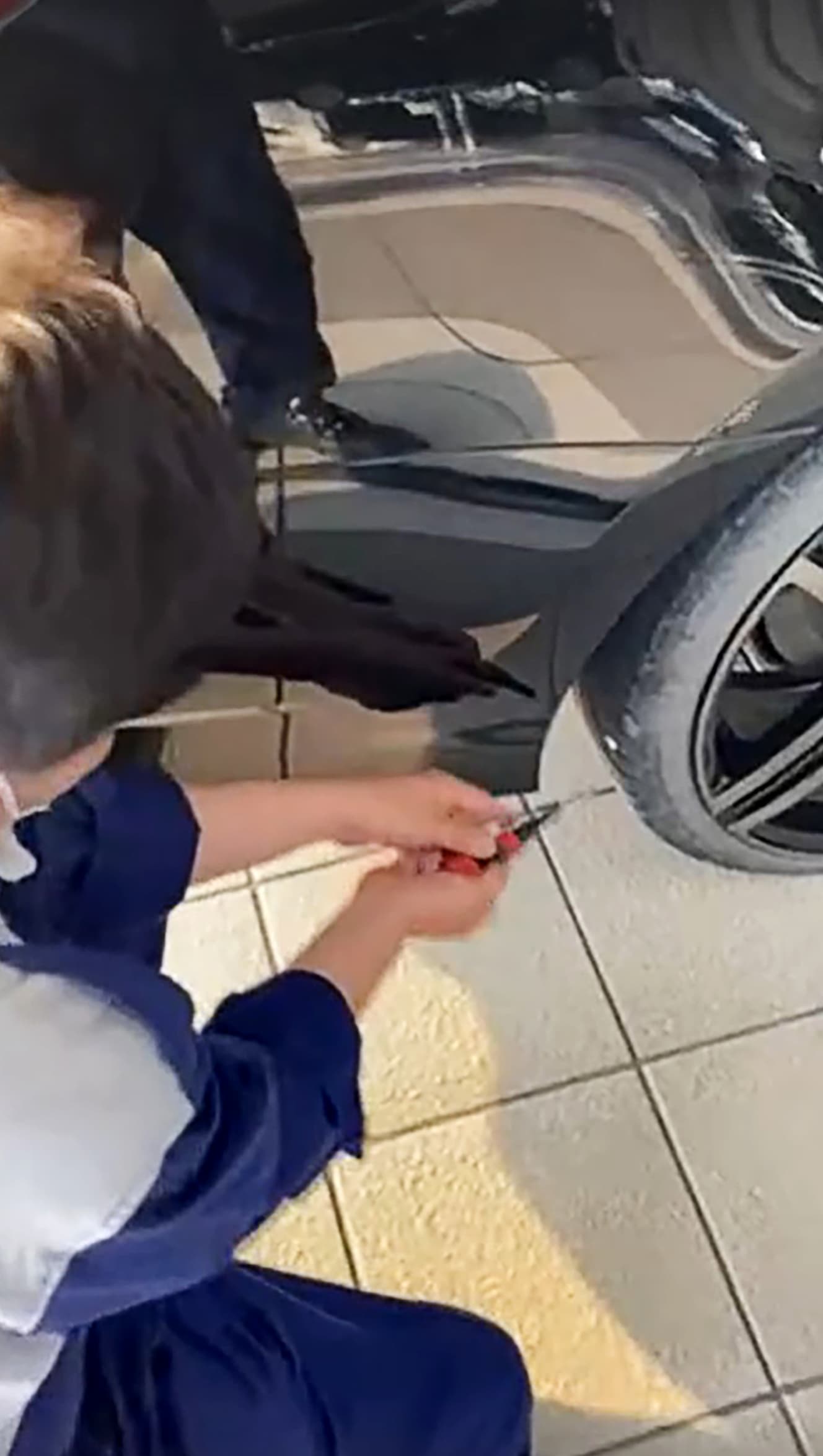
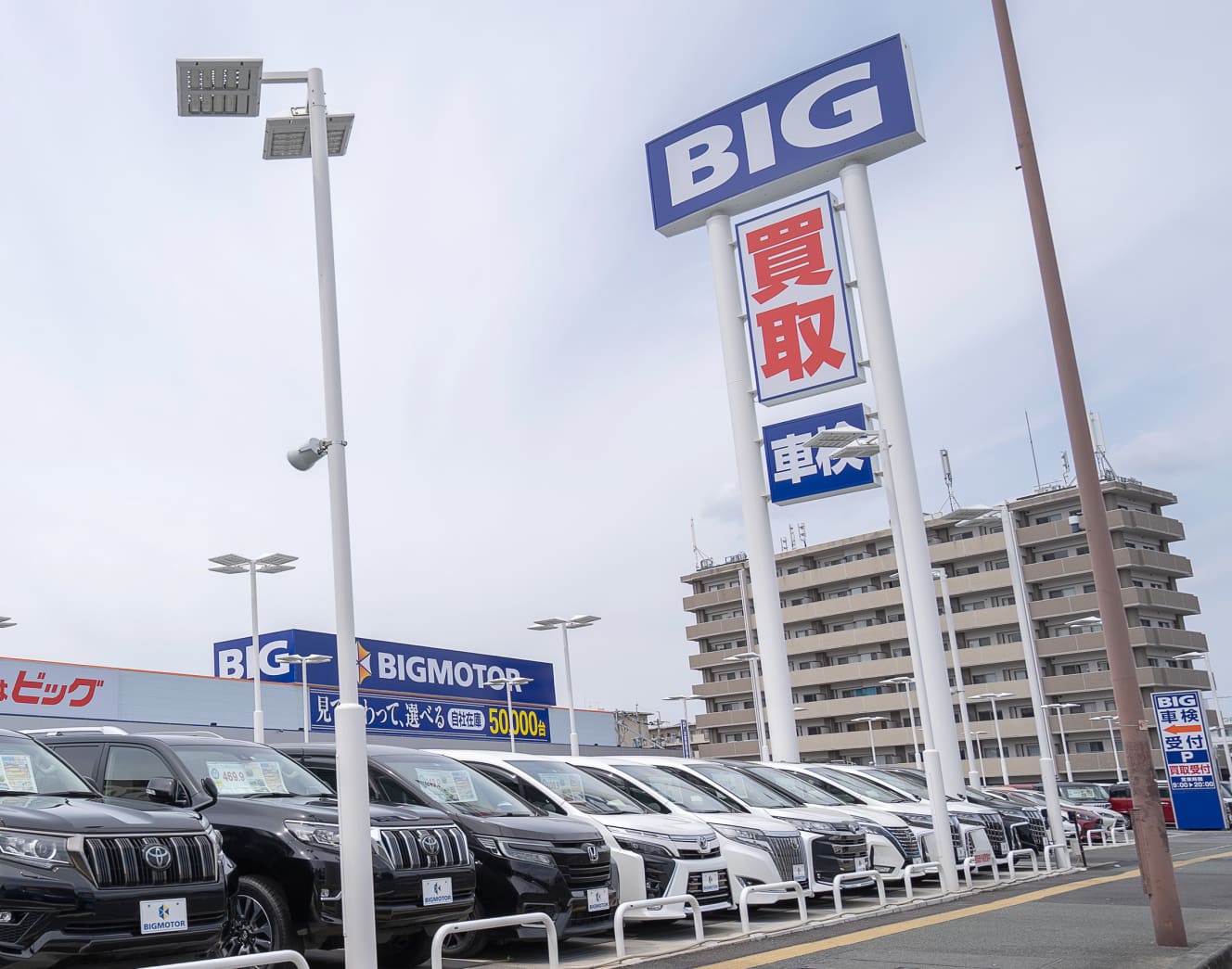
Rampant Fraudulent Vehicle Inspections
Mr. A says that there were other irregularities that took place at the Kumamoto Hamasen branch. In particular, he says, vehicle inspections were a hotbed of fraud.
One of the irregularities that took place in vehicle inspections was inspections by unqualified personnel. Various qualifications are required for vehicle inspection certification, and it is forbidden for ordinary mechanics to perform these inspections. However, at the Kumamoto Hamasen branch, it was common practice for inspections to be performed by unqualified mechanics and for the names of qualified personnel to be written on the documents in their place. It was common practice to change the oil for gadgets used to lubricate gears, etc., with only one liter of oil in order to keep the volume to a minimum. On the mechanics’ communication group lines, I often saw exchanges of messages such as, ‘It’s OK to have the oil changed,’ or ‘It’s a perfect crime.
According to an announcement by the Kyushu District Transport Bureau in March of this year, the Kumamoto Hamasen branch had issued safety standard conformity certificates to 58 vehicles from December 2008, when records were kept, without conducting speed meter inspections. However, Mr. A revealed that the number of vehicles in which various irregularities were committed was no less than 1,000 during the period alone.
Why is fraud so rampant? One reason is the unreasonable quotas set by the head office.
The quota for vehicle inspections was set based on the previous year, and at the Kumamoto Hamasen branch, the monthly average was set at 170 to 180 vehicles. However, there were only seven to eight mechanics. This is an absolutely impossible number of mechanics, and other large factories of the same size have at least 10 mechanics.
In order to achieve the quota, the designated factories also performed “pre-inspection and post-maintenance,” which is prohibited by the Ministry of Land, Infrastructure, Transport and Tourism. A designated factory is a factory that is authorized by the government to perform all processes of vehicle inspections. Normally, the vehicle is inspected after it has been fully serviced, but in months when we could not meet our quota, we moved up the next month’s vehicle inspection without the customer’s permission, and only the parts that were faulty were serviced afterwards. In order to meet the quota, they had no choice but to cheat while cutting costs and labor.
Finally, Mr. A expressed his anger.
What I find most unforgivable is the attitude of the head office that ‘no specific instructions were given’ regarding the numerous irregularities and quotas. If sales were poor, the factory manager would be criticized by name in front of other factory managers. People from the head office would come to the branch every month to inspect the situation, but they would turn a blind eye to the plight of the factory floor. That was the hardest part for me.
The astonishing number of irregularities that were taking place behind the scenes of a large corporation. …… What does the head office of Big Motor think about these facts? We sent a letter of inquiry to the company, but received no response by the deadline. We also visited the home of Hiroyuki Kaneshige, 72, the president and representative director, in Tokyo to ask for his opinion, but again received no response. Kumiko Kato, an automotive journalist with extensive knowledge of the auto industry, asserted, “Big Motor is a company whose president Kaneshige is a big fan.
Big Motor is a company that President Kaneshige grew in his own lifetime. Almost all of its branches nationwide are equipped with designated factories that can perform vehicle inspections on their own, and the company has grown rapidly over the past decade or so. Somewhere along the way, I think the company’s structure changed to one of profit supremacy. These irregularities must be dealt with promptly and thoroughly. In particular, fraudulent vehicle inspections directly affect the lives of drivers and must not be tolerated.
If the head office had been aware of the situation and had taken no action, it would be unforgivable.

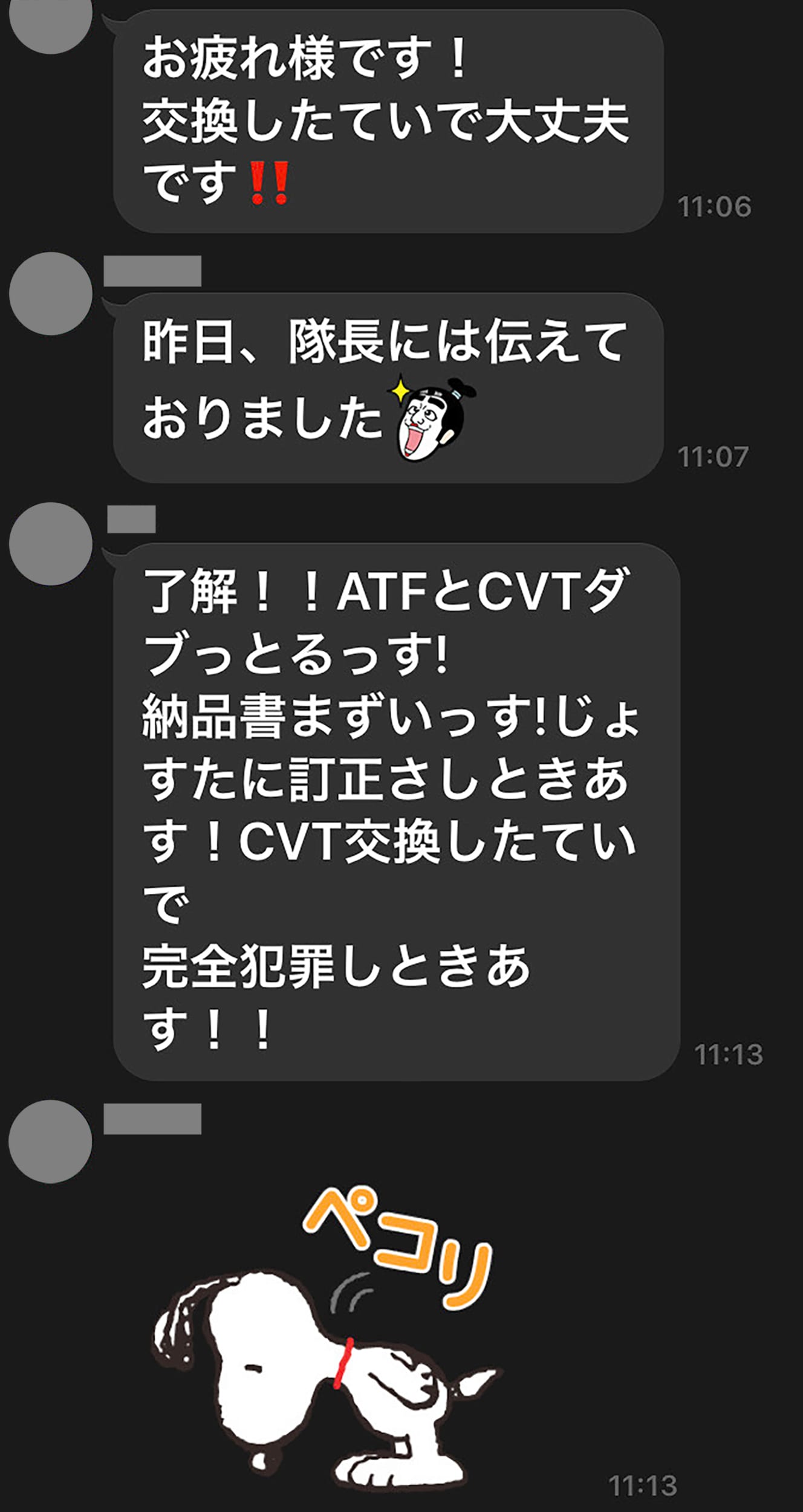
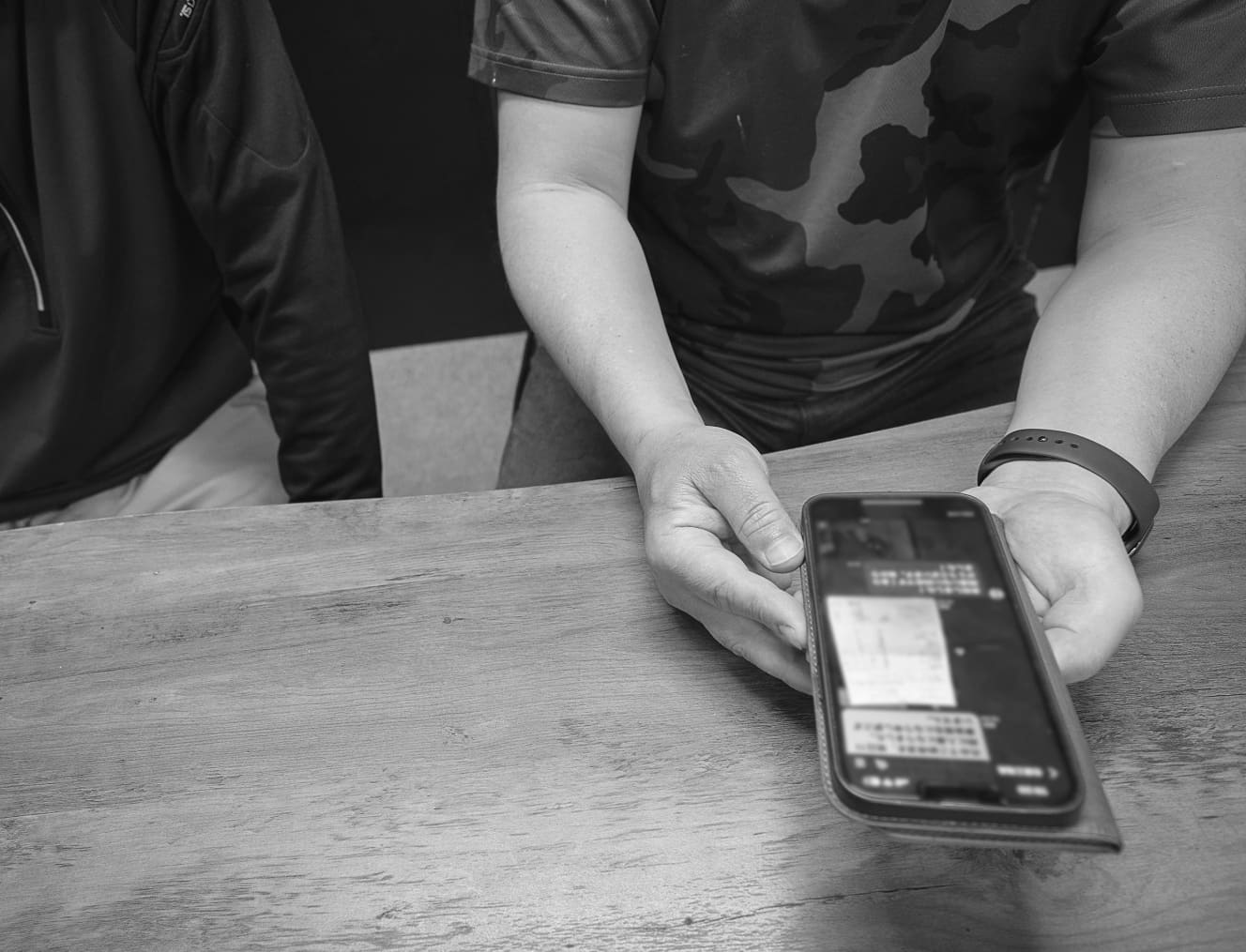
From the May 5, 2023 issue of FRIDAY
PHOTO: Hiroto Kato (Kumamoto Hamasen store exterior, portrait photo) Courtesy of Mr. A (video, documents, line screen)